OT Security – Introduction – OT Overview
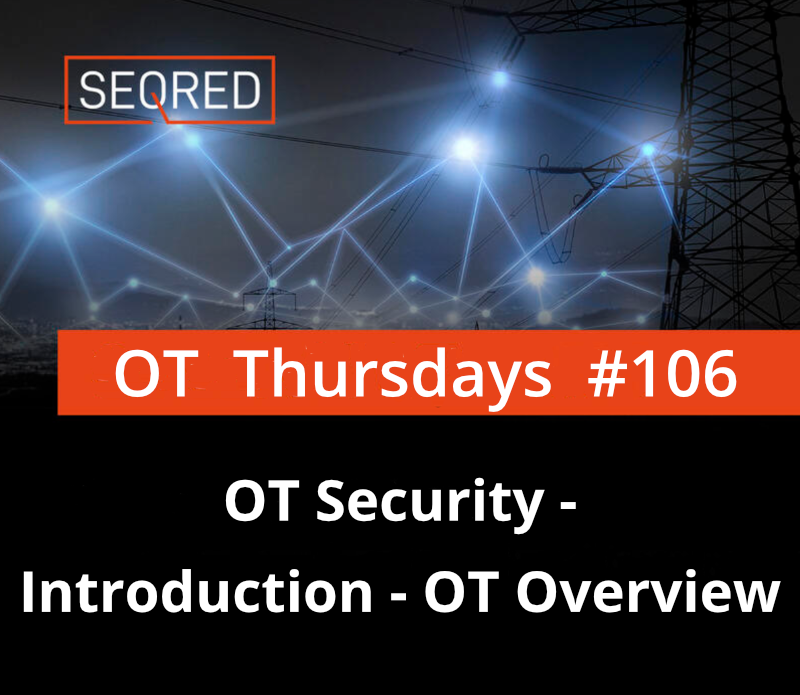
OT Overview
Operational technology (OT) refers to a diverse range of programmable systems and devices that interact with the physical world, either directly or by managing devices that do. These systems and devices can detect or cause changes in devices, processes, and events through monitoring and control. Examples of OT systems include industrial control systems, building automation systems, transportation systems, physical access control systems, physical environment monitoring systems, and physical environment measurement systems.
OT systems consist of various control components, such as electrical, mechanical, hydraulic, and pneumatic components that work together to achieve a specific objective, such as manufacturing or energy transportation. The process is part of the system that is primarily concerned with producing an output, while the controller (or control) is responsible for maintaining conformity with specifications. The control components of the system determine the desired output or performance.
OT systems can be configured in one of three ways: open-loop, closed-loop, or manual mode.
- In an open-loop configuration, the output is controlled by established settings.
- In a closed-loop configuration, the output influences the input to maintain the desired control objective.
- In manual mode, the system is entirely controlled by humans.
Various types of OT systems are commonly used, including supervisory control and data acquisition (SCADA), distributed control systems (DCS), programmable logic controllers (PLCs), building automation systems (BAS), physical access control systems (PACS), and the Industrial Internet of Things (IIoT).
Evolution of OT
Today’s OT has largely evolved by incorporating IT capabilities into existing physical systems, often replacing, or supplementing physical control mechanisms. For instance, embedded digital controls have replaced analogue mechanical controls in rotating machines and engines. The evolution of OT has been encouraged by improvements in cost and performance, resulting in the development of many “smart” technologies, such as the smart electric grid, smart transportation, smart buildings, smart manufacturing, and the Internet of Things. While this enhances the connectivity and criticality of these systems, it also creates a greater need for adaptability, resilience, safety, and security.
To address the safety issue, the evolution of OT has led to the development of new security standards, measures, and technologies such as the IEC 62443 series of international standards for cybersecurity in industrial automation and control systems (IACS), also known as operational technology (OT) systems. The standard was developed by the International Electrotechnical Commission (IEC) to provide a comprehensive framework for securing IACS from cyber threats and provides guidance for all stages of the IACS lifecycle, from design and development to installation, operation, and maintenance. They address a wide range of cybersecurity issues, including network security, system hardening, access control, secure coding, security testing, incident response, and recovery.
The IEC 62443 standards are widely recognized and used by organizations around the world to ensure the security and reliability of their IACS. Compliance with the standards can help organizations to protect their IACS from cyber threats, prevent system downtime and data loss, and comply with regulatory requirements.
In addition to the IEC 62443 standards, other security standards and frameworks may also be relevant to IACS cybersecurity, including the NIST Cybersecurity Framework, ISO/IEC 27001, and ISA/IEC 62443.
The engineering of OT systems continues to evolve, providing new capabilities while maintaining the typical long-life cycles of these systems. The incorporation of IT capabilities into physical systems leads to emergent behaviour that may have security implications. Engineering models and analysis are evolving to address these emergent properties, including safety, security, privacy, and environmental impact interdependencies.
OT-Based Systems and Their Interdependencies
OT is used in many industries and critical infrastructures (in bold), such as:
Chemical Sector
Commercial Facilities Sector
Communications Sector
Critical Manufacturing Sector
Dams Sector
Defense Industrial Base Sector
Emergency Services Sector
Energy Sector
Financial Services Sector
Food and Agriculture Sector
Government Facilities Sector
Healthcare and Public Health Sector
Information Technology Sector
Nuclear Reactors, Materials, and Waste Sector
Transportation Systems Sector
Water and Wastewater Systems Sector
In many countries, OT plays a critical role in the operation of interdependent critical infrastructures. It is important to note that while some governmental agencies operate many of the critical infrastructures mentioned above, many others are privately owned and operated. Critical infrastructures are often referred to as a “system of systems” due to the interdependencies that exist between various industrial sectors and the interconnections between business partners. These infrastructures are highly interconnected and mutually dependent in complex ways, both physically and through information and communications technologies. An incident in one infrastructure can, directly and indirectly, affect other infrastructures through cascading and escalating failures.
For example, the electrical power transmission and distribution grid industries use geographically distributed SCADA control technology to operate highly interconnected and dynamic systems consisting of thousands of public and private utilities and rural cooperatives for supplying electricity to end-users. Some SCADA systems monitor and control electricity distribution by collecting data from and issuing commands to geographically remote field control stations from a centralized location. SCADA systems are also used to monitor and control water, oil, and natural gas distribution, including pipelines, ships, trucks, and rail systems, as well as wastewater collection systems.
SCADA systems and DCS are often networked together. This is the case for electric power control centres and electric power generation facilities. Although electric power generation facility operation is controlled by a DCS, the DCS must communicate with the SCADA system to coordinate production output with transmission and distribution demands.
Electric power is often regarded as one of the most prevalent sources of disruptions of interdependent critical infrastructures. For instance, a cascading failure can be initiated by a disruption of the microwave communications network used for an electric power transmission SCADA system. The lack of monitoring and control capabilities could cause a large generating unit to be taken offline, an event that would lead to a power loss at a transmission substation. This loss could cause a major imbalance, triggering a cascading failure across the power grid. This could result in large area blackouts that could potentially affect oil and natural gas production, refinery operations, water treatment systems, wastewater collection systems, and pipeline transport systems that rely on the grid for electric power.
0 Comments